Production
Optimal in-house Production
Staehle produces aerosol cans completely in-house. From tin plate printing, cutting the sheets for the bodies with a precision of 50 μm, to pressing and shaping tops and bottoms and to bonding the parts in a fully automatic process that includes inline testing and finally packaging – if required on euro pallets with tray packaging or multi-layered packaging or on industrial pallets with multi-layered packaging.
The necessary process stability is down to modern machines, a close meshing of the individual production steps and, decisively, well-trained employees who commit themselves daily to the quality of the products, the keeping to deadlines and the assured implementation of specific requirements.
Fabrication
Integrated Processes
Tin welding for aerosol cans is linked with the highest standards of weld stability and leak tightness. For instance, Staehle only uses machinery made by leading manufacturers which is then operated by specialists with a trained eye for details. Therefore, fully automatic lines are in place to seam tops, bodies and bottoms. And the in-house automation technology department has, for example, developed robot cells which remove components from the machines and sort them into trays. The feeding of the components is also done fully automatically – for safe, integrated processes.
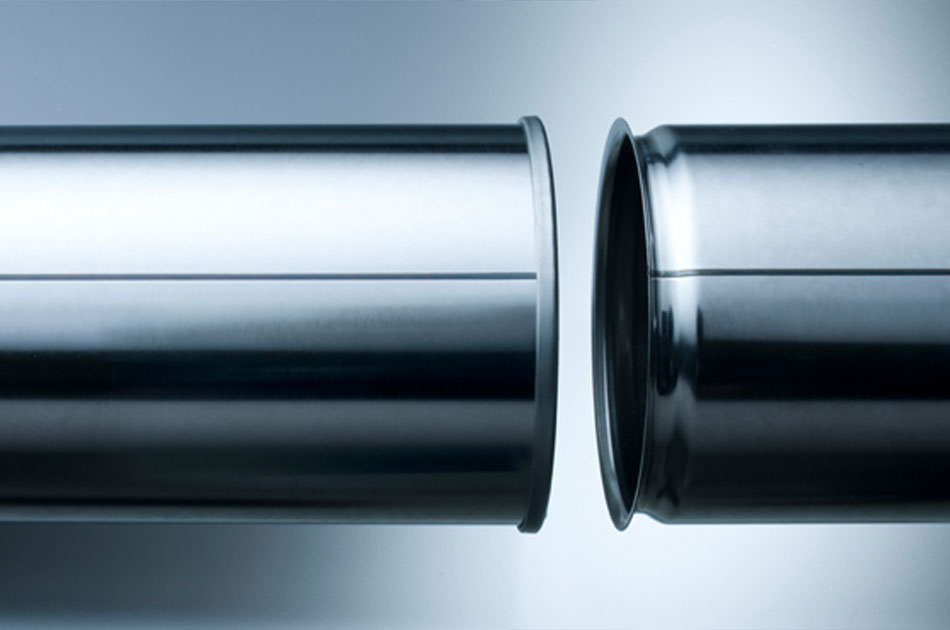
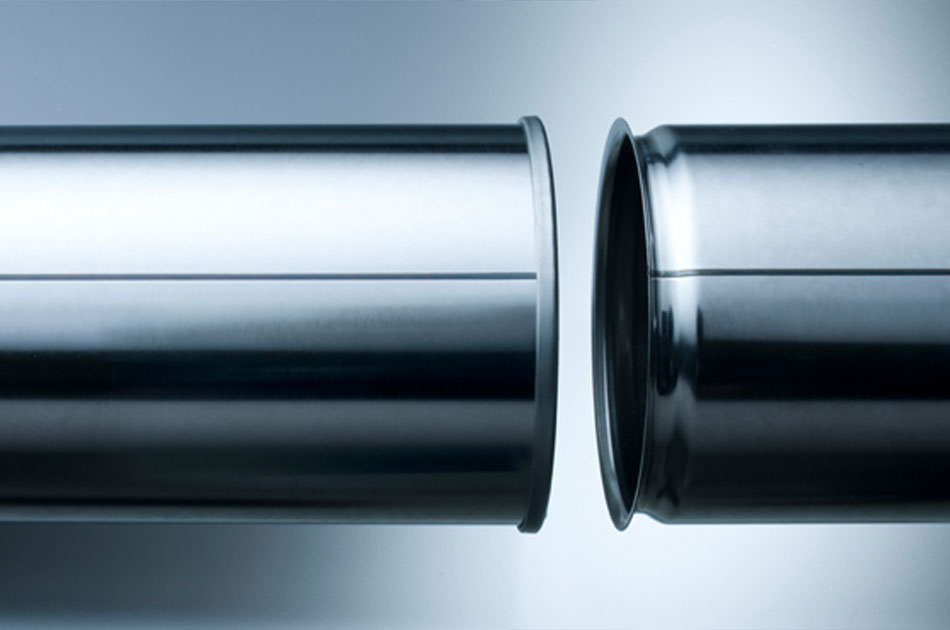
Fabrication
Integrated Processes
Tin welding for aerosol cans is linked with the highest standards of weld stability and leak tightness. For instance, Staehle only uses machinery made by leading manufacturers which is then operated by specialists with a trained eye for details. Therefore, fully automatic lines are in place to seam tops, bodies and bottoms. And the in-house automation technology department has, for example, developed robot cells which remove components from the machines and sort them into trays. The feeding of the components is also done fully automatically – for safe, integrated processes.
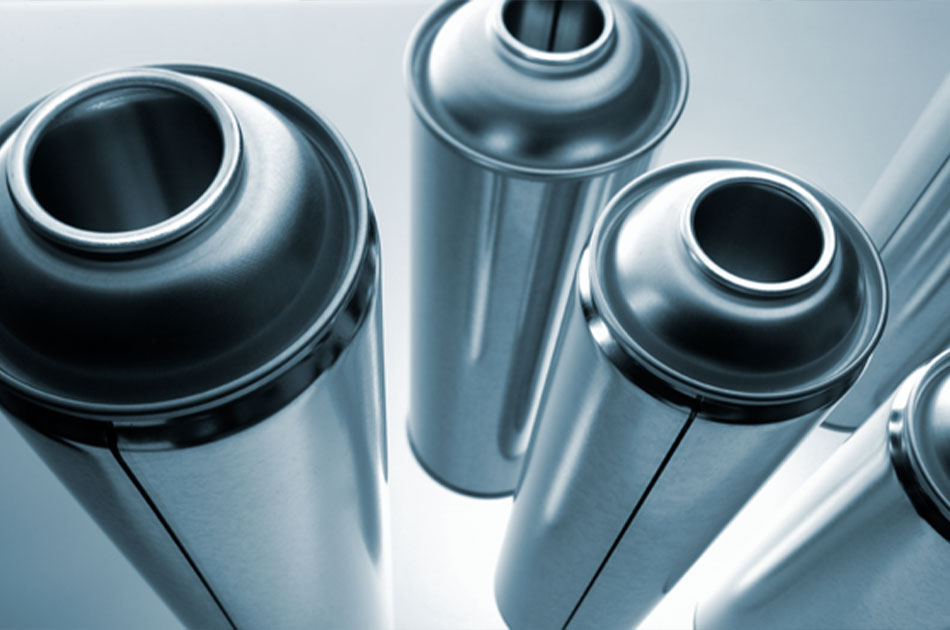
Tool Making
Pleased to be a Systems Provider
Body, top, bottom – the three pieces that go together to make Staehle aerosol cans. Basically simple – but nevertheless complex: as body sheets
have, in the main, already been printed, the lacquer not only has to be elastic and the shaping tools precise, the latter also has to have a high degree of surface hardness, especially when manufacturing large runs. Tools and format parts for the fabrication of Staehle aerosol cans are therefore made in the in-house tool-making department. The concentrated experience and expertise in this sector makes Staehle a potential partner and not just for the production of aerosol cans. For example, as a systems provider for every component in a 2-chamber can – from the can to the plastic cartridge and the twist mechanism, Staehle offers all the services from one source. Or Staehle, together with the customer, develops innovative products out of thin tin plate – from the initial design studies and the making of a prototype right up to series production.
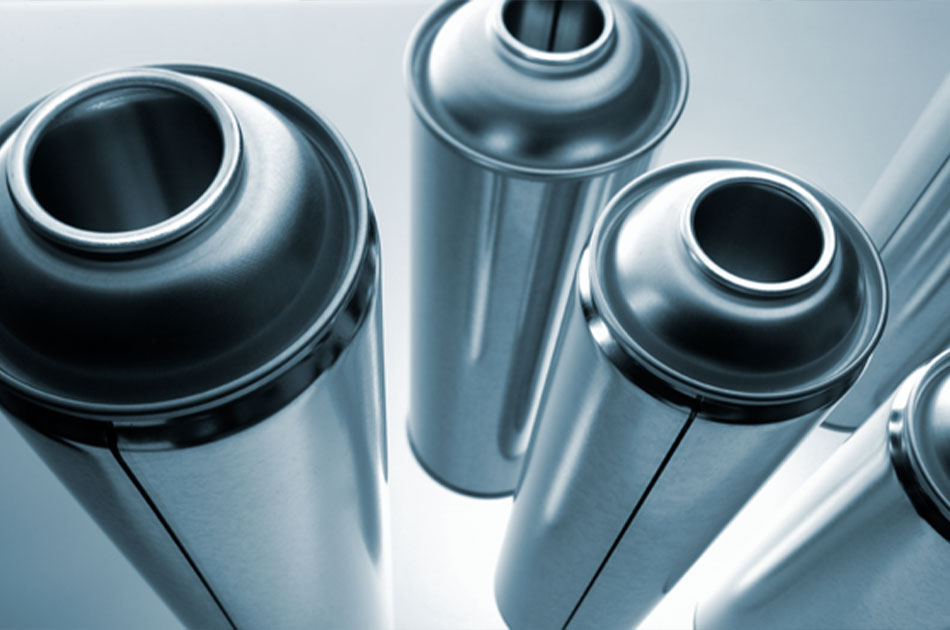
Tool Making
Pleased to be a Systems Provider
Body, top, bottom – the three pieces that go together to make Staehle aerosol cans. Basically simple – but nevertheless complex: as body sheets
have, in the main, already been printed, the lacquer not only has to be elastic and the shaping tools precise, the latter also has to have a high degree of surface hardness, especially when manufacturing large runs. Tools and format parts for the fabrication of Staehle aerosol cans are therefore made in the in-house tool-making department. The concentrated experience and expertise in this sector makes Staehle a potential partner and not just for the production of aerosol cans. For example, as a systems provider for every component in a 2-chamber can – from the can to the plastic cartridge and the twist mechanism, Staehle offers all the services from one source. Or Staehle, together with the customer, develops innovative products out of thin tin plate – from the initial design studies and the making of a prototype right up to series production.
Printing
Brand Worlds on Metal
Pre-press, production print, white coatings, protective coatings for the exterior look, interior coating for corrosion protection – all the processes take place in Staehle’s in-house printing facility. In order for the final print to exactly match the customers’ ideas, Staehle creates a tin proof with original lacquers and colours on a digital colour proof system – with all the nuances of the subsequent print run and the identical appearance of the print on the metal surface. The print and paint shops meet current technological and ecological standards and only high-quality inks and lacquers are used.
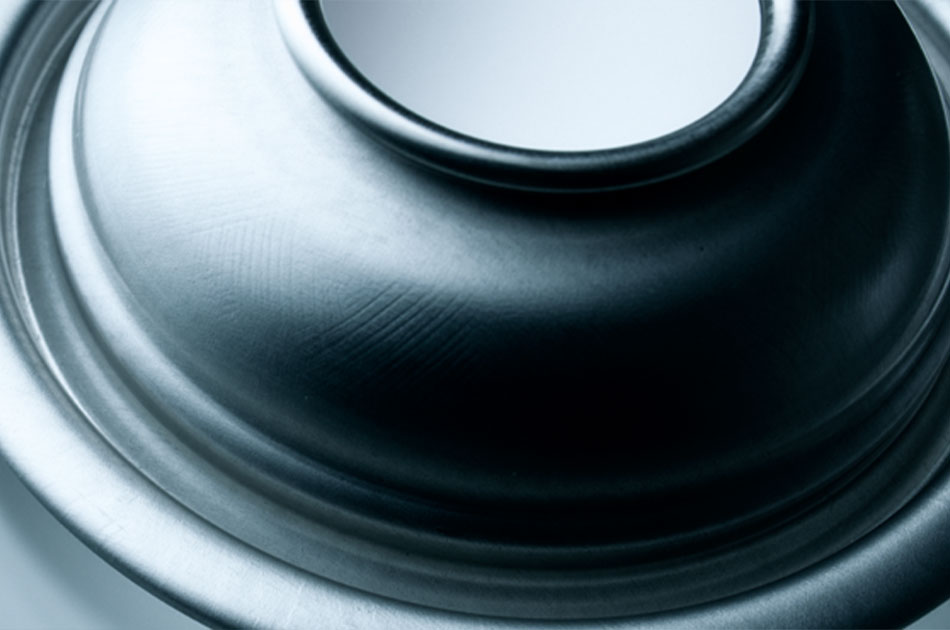
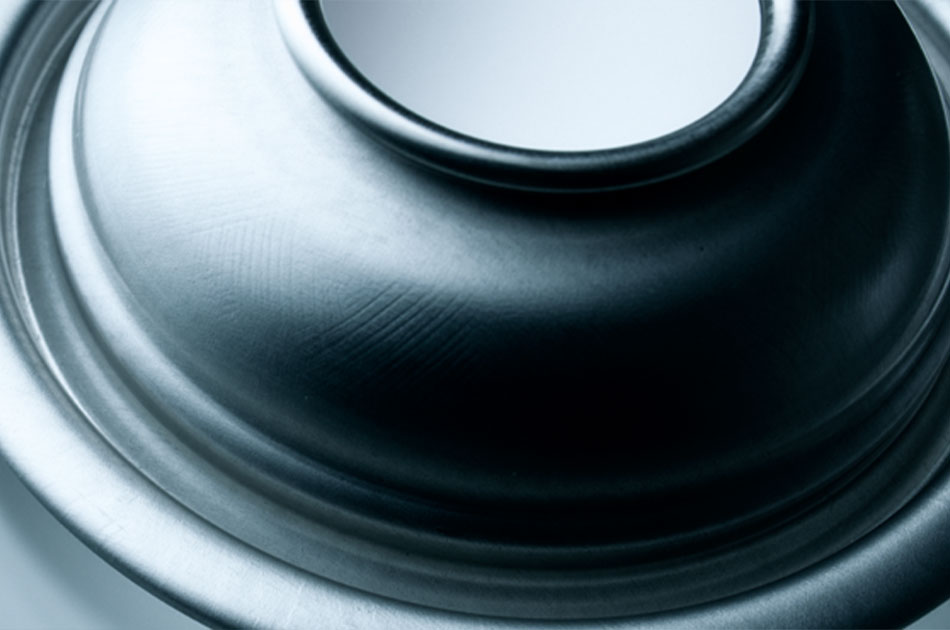
Printing
Brand Worlds on Metal
Pre-press, production print, white coatings, protective coatings for the exterior look, interior coating for corrosion protection – all the processes take place in Staehle’s in-house printing facility. In order for the final print to exactly match the customers’ ideas, Staehle creates a tin proof with original lacquers and colours on a digital colour proof system – with all the nuances of the subsequent print run and the identical appearance of the print on the metal surface. The print and paint shops meet current technological and ecological standards and only high-quality inks and lacquers are used.
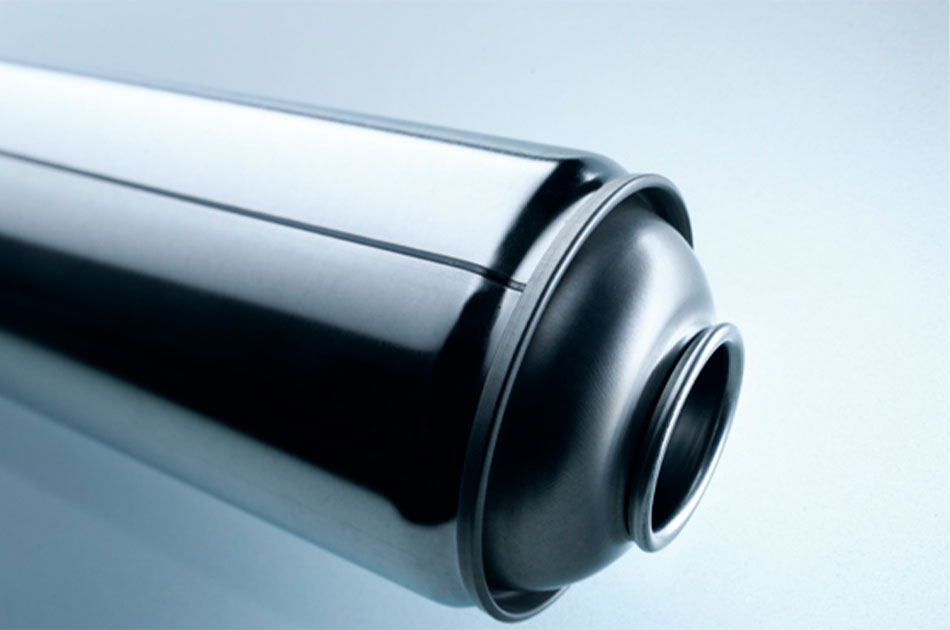
Quality
Made in Germany
One Staehle aerosol can is exactly like the other: of the highest product quality. This is backed up not only by certification of the whole fabrication in accordance with the DIN EN ISO 9001 standard, but also by full in-line testing of components and finished cans. When producing tops and bottoms, camera inspection systems test the correct, consistent injection of the compound. Testing the cans for pressure resistance and micro leakage is also done in-line on high-pressure testers that have been optimised together with the manufacturers. It means even minimal irregularities are recognised without fail, and faulty products are immediately discharged from the process. Additional buckling and bursting testing is carried out in the quality laboratory, as are seam measurements with high-resolution cameras. All the recorded data is archived and can be made available to customers in a quality report upon desire. As a result, only top grade cans leave the company. The optional printing of cans with a UV coding assures complete tracking and tracing of the products in accordance with the latest guidelines.
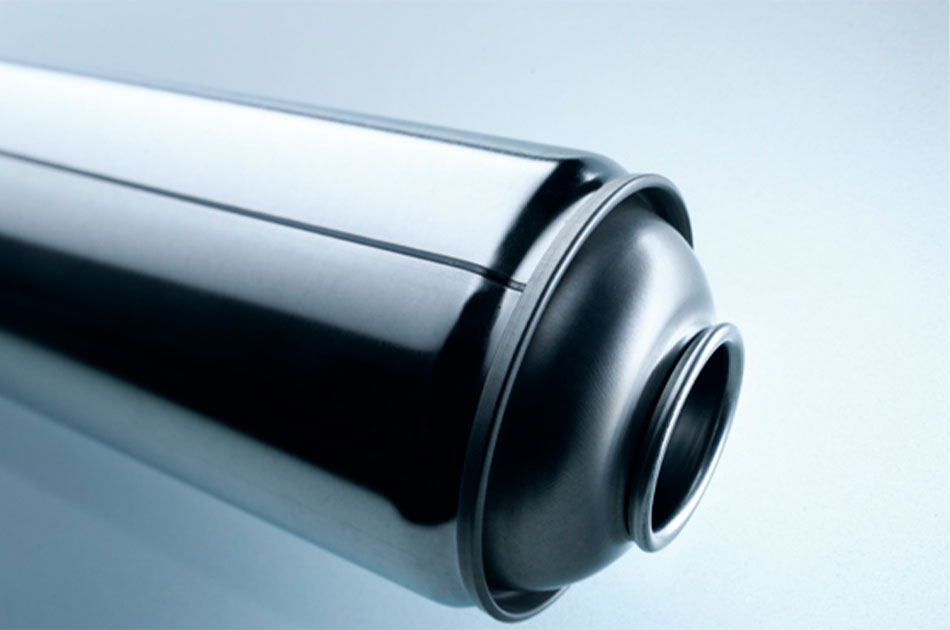
Quality
Made in Germany
One Staehle aerosol can is exactly like the other: of the highest product quality. This is backed up not only by certification of the whole fabrication in accordance with the DIN EN ISO 9001 standard, but also by full in-line testing of components and finished cans. When producing tops and bottoms, camera inspection systems test the correct, consistent injection of the compound. Testing the cans for pressure resistance and micro leakage is also done in-line on high-pressure testers that have been optimised together with the manufacturers. It means even minimal irregularities are recognised without fail, and faulty products are immediately discharged from the process. Additional buckling and bursting testing is carried out in the quality laboratory, as are seam measurements with high-resolution cameras. All the recorded data is archived and can be made available to customers in a quality report upon desire. As a result, only top grade cans leave the company. The optional printing of cans with a UV coding assures complete tracking and tracing of the products in accordance with the latest guidelines.